As granny flats have been on the rise, there has been an increase in companies that specialize in ADU construction.
What most people don’t realize is that these construction companies tend to specialize in a specific type of ADU construction.
And yes, there are different ways to build the little granny flat in your backyard.
We have the traditional stick-built ADU, but prefab ADUs are another great option, specifically modular or panelized prefabs. You might have even seen some companies dabbling in 3D printed granny flats — we aren’t holding our breath!
Modular Construction
There are two types of prefabricated building techniques
The first is modular.
With this technique, the whole ADU is built in a factory, then transported to your backyard and lifted onto the pre-built foundation.
The companies construct the ADUs in box-like modules with attached walls, floors, ceilings, plumbing, and interior fixtures. A crane then lifts the modules and places them onto the foundation.
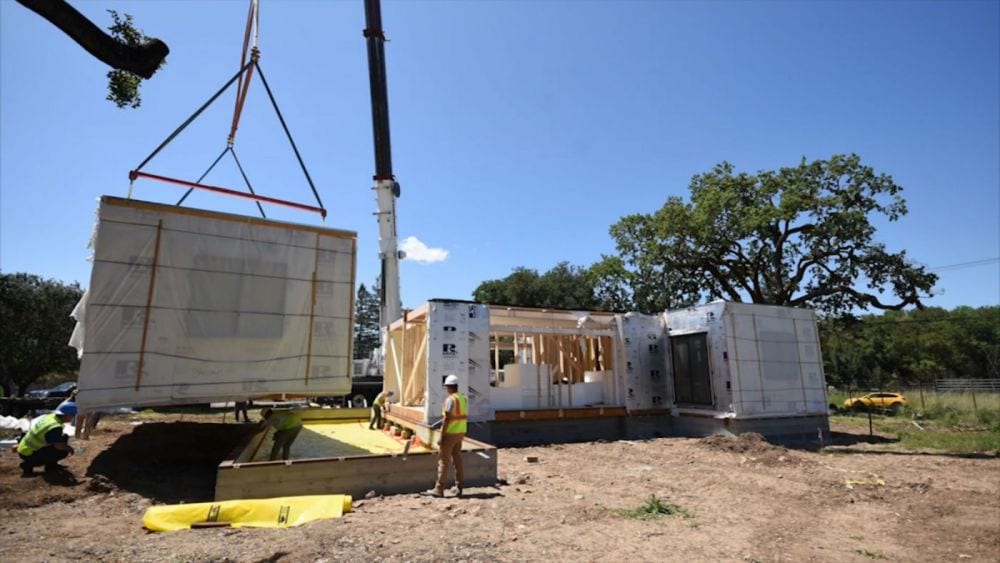
ABC News
Panelized Construction
Panelized construction is the second type of prefab building technique.
Here, the framing package is being built in a factory and shipped on-site to be assembled. Panelized construction is different than modular construction in a few ways.
- With panelized construction, companies build only the exterior shell of the ADU at the factory, and the shell is broken down into flat panels that can stack on a flat-bed. These panels are assembled on a pre-built foundation, just as the modules are with modular construction.
- Unlike modular prefabs, panelized prefabs do not have the interior and exterior finishes already assembled, nor does it have additional components, such as plumbing, already installed. These finishes happen once the panels have been assembled on-site.
- Modular construction and panelized construction are appraised in different ways. Panelized will appraise the same way traditional site-built house will, but modular construction will usually appraise lower.
- Modular is not customizable. You can choose from a few floor plans, but the walls, windows, and doors cannot be moved. Nor can you rearrange rooms like a bathroom or a kitchen.
- We love panelized because you can reap some of the cost benefits of having your framing package built in a factory, yet you still can customize your ADU to make it exactly what you want.
Stick-Built Granny Flats
The final method is stick-built, which is the main alternative to the two prefab methods listed above.
A stick-built granny flat is traditionally built from wood directly onto the site. In this case, “on-site” would be your backyard.
Most people aren’t too informed on the other building methods, which is why they choose to go with a stick-build. However, it is important to understand the benefits that each offers before making your decision.
Maxable offers a free ADU Planning Phone Call, in which one of our team members can help you decide which option would be right for you. We also can connect you to general contractors and architects that specialize in whichever option you choose.
For now, let’s take a look at a few differences between these types of ADU building techniques.
What is the Difference in Durability Between Stick-Builds and Prefab ADUs?
Some people assume that prefabs lack durability when they think about how companies build them and how quickly they assemble them.
The truth is, prefabs are actually more durable than stick-builds.
Prefab manufacturers actually have to make them more durable than a traditional stick-built ADU due to the process they undergo.
The panels or modules that make up the prefabs have to be transported on a truck traveling 60 miles per hour, then lifted off the truck and onto the foundation by a crane.
With all that moving and rattling that happens in this process, prefabs prove their durability prior to even being completed.
Do Prefab ADUs Add the Same Value to Homes as Stick-Built ADUs?
While prefab ADUs do add value to your home, they do not add quite as much value as the average stick-built ADU does.
However, there is a way around this.
Hybrids.
You can combine a prefab building technique with the traditional stick-built building techniques to produce a hybrid ADU. The beauty of this is that hybrid ADUs appraise the same as a pure stick-built ADU.
Depending on your property and ADU, building a hybrid could potentially be more cost-effective as well.
Are Prefab ADUs Cheaper Than Stick-Built ADUs?
Prices obviously fluctuate for each individual ADU and property, so it is difficult to give a firm answer to this question.
When first looking at costs, prefabs seem to always be the cheaper option. With prefabs, you save money on construction and labor, and the materials can even be cheaper.
However, you must factor in other costs that come with prefabs, such as transportation and crane costs.
In general, most prefab ADUs tend to be a bit cheaper to build, but not always by much. And again, it all depends on the individual ADU and property.
For help on deciding what is the best route given your personal situation, book a free ADU Planning Phone Call with one of our Maxable team members!
Steel vs. Wood
One way to make building a prefab cheaper, especially with panelized construction, is by using steel.
Prefab ADUs are making a big move toward steel, rather than the traditional wood build, for several reasons. Steel prefabs outdo wood prefabs in the following areas:
- Cost
- Construction time
- Durability
- Sustainability
Cost
Using steel instead of wood costs up to 50% less in framing construction. If you use steel, you will need less material, as well as less labor.
Construction Time
Teams have to build wood-framed buildings by hand, which means they require skilled laborers who know how to cut it to size, frame it, drill holes, etc.
Construction companies that specialize in steel have framing technologies, which results in a faster process, and it eliminates the need for skilled laborers that wood-frames require.
Building a steel-framed ADU will require less material and less labor (due to the framing technology), and these two factors contribute to the lower cost and the faster construction time.
Durability
With all the earthquakes and fires that California experiences, chances are, we want a sturdy ADU.
Wood obviously burns down in a fire, but steel, on the other hand, is non-combustible.
Not only is steel more likely to survive a fire, but it is also more durable than wood in general. Steel is resistant to moisture, mold, termites, rust, and warping.
Sustainability
Reduce, reuse, recycle.
When it comes to sustainability, steel checks all the boxes.
We already know that we “reduce” with steel because we can use less material.
Now let’s take a look at “reuse” and “recycle.” Recycled products make up 88% of structural steel, and structural steel can be fully recycled at the end of its life.
Also, at the end of construction, wood leaves about 20% waste, whereas steel only leaves about 2%.
Due to these benefits in cost, time, durability, and sustainability, a steel-framed prefab ADU could be the way to go.
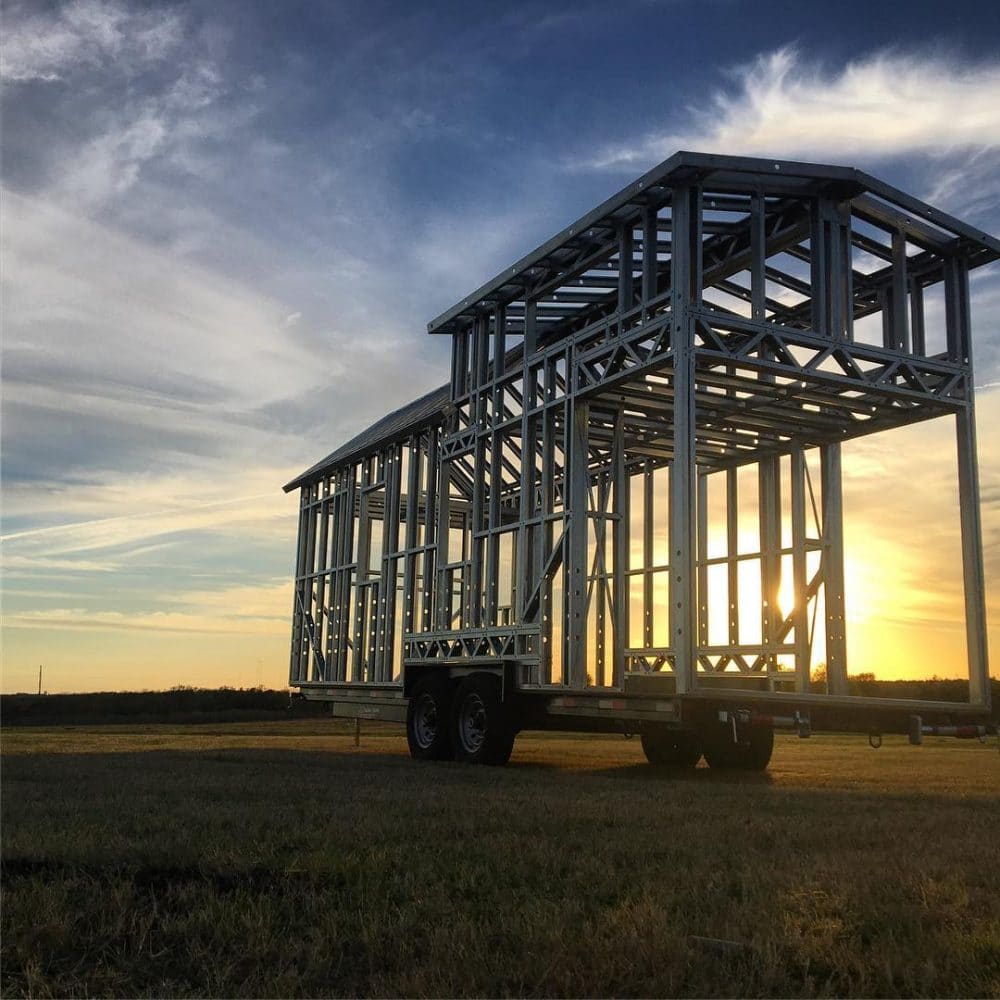
Tiny House Design
Quick Overview
Modular prefabs, panelized prefabs, and stick-builds are the three main ADU building techniques.
While stick-builds and prefabs each have their different benefits, prefabs have been gaining traction in the ADU world.
If you’re interested in building a granny flat on your property and need help making decisions, such as these, book a free phone consultation with Maxable!
We will be able to give you the information you need to get started, as well as connect you to the contractors and architects that will best suit your project.