What is a panelized modular ADU?
We are currently in the golden age of prefab (prefabricated) ADU design, so there’s really no time like the present to consider adding a panelized modular ADU to your property! They are definitely a top-notch choice within the prefab industry, and we fully expect to see their popularity continue to rise this year.
So, what are they? Panelized modular ADUs are a type of prefab construction where the framework (walls and roof with windows and electrical already installed) is constructed off-site in a factory and later shipped to your property on a flatbed truck. Once all the pieces arrive, everything is assembled and finished in as little as three months. Quite the prime example of ADU innovation!
That being said, it’s important to make sure that they’re the right choice for you and your property. So, with special insight provided by Ryan Jantz, co-founder of Proteus Homes, consider this your personal guide to everything panelized modular.
Let’s get started!
What is the difference between panelized modular vs. traditional prefab vs. custom stick build?
With all the ADU options out there, we understand it can get confusing. So, let’s take a minute to distinguish panelized modular ADUs from traditional prefabs and custom stick builds.
Traditional prefab
These types of ADUs differ from panelized modular constructions because the entire structure is built in a factory and then transported to your property. By the time it is rolled onto the site or lifted into place via crane, all it needs is some utility connections and some final touches and it should be ready for move-in as early as a week.
The biggest drawback, however, is that customization is very limited. Your selected prefab company will usually have a catalog of ADU designs that you can choose from. If none of those will work for your lot or needs, you’re out of luck.
Stick-build
Custom stick builds are the opposite of traditional prefabs in that they are built entirely on-site, from the foundation to the roof; no part of the ADU is built in a factory. This means that all the construction happens on your property. This allows for full customization and retrofitting to your lot, but construction time is lengthy, often lasting anywhere between 8-10 months.
Panelized modular
Panelized modular meets in the middle of traditional prefab and custom stick-build. Although not as fast as traditional prefab, panelized modular still cuts down the construction time significantly while still allowing customization.
The wall panels of your unit are constructed off-site in a factory, then shipped to your property where everything is assembled. Once all of the walls and roof are erected, the remainder of the work is similar to traditional construction where they install insulation, drywall, finishes, etc.
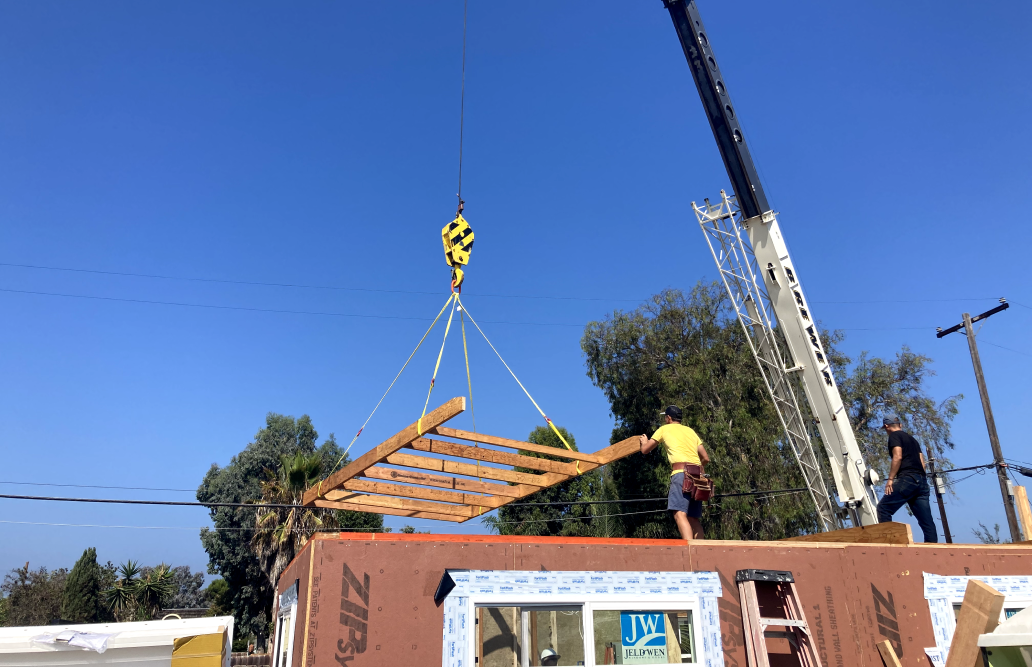
Photo courtesy of Proteus Homes
What are the advantages of panelized modular ADUs?
As we mentioned before, panelized modular ADUs are a fantastic in-between option for homeowners who like aspects of both traditional prefabs and custom stick builds since there is both factory and on-site construction involved.
But that’s not all! Here are some other key advantages that they offer.
Greater customization
If you’re someone who loves a good design project, then look no further than panelized modular ADUs. Similar to stick build, they are completely customizable. There are virtually no design limitations since the pieces are easily shipped on a flatbed; pretty much any size, shape, and style is doable. As long as your lot characteristics and budget can comply, the sky is your limit!
This is in stark contrast to traditional prefabs where you’re somewhat limited in the design and style of the home. Since a traditional prefab ADU would need to be transported onto your property, likely via the highway, two stories are not typically an option. Stucco-sided homes are also uncommon for traditional prefabs.
Just know that high levels of customization come with extended timelines and inflated price tags. Straying from the more simplistic floor plans will take more time and money to construct. But for some homeowners, it’s more than worth it!
And if you’re looking for a happy medium? Go with a semi-custom approach! Panelized prefab companies typically offer a wide range of floor plans to choose from. Once you pick one, simply customize the layout to your liking. This hybrid option keeps time and costs down.
Faster construction time
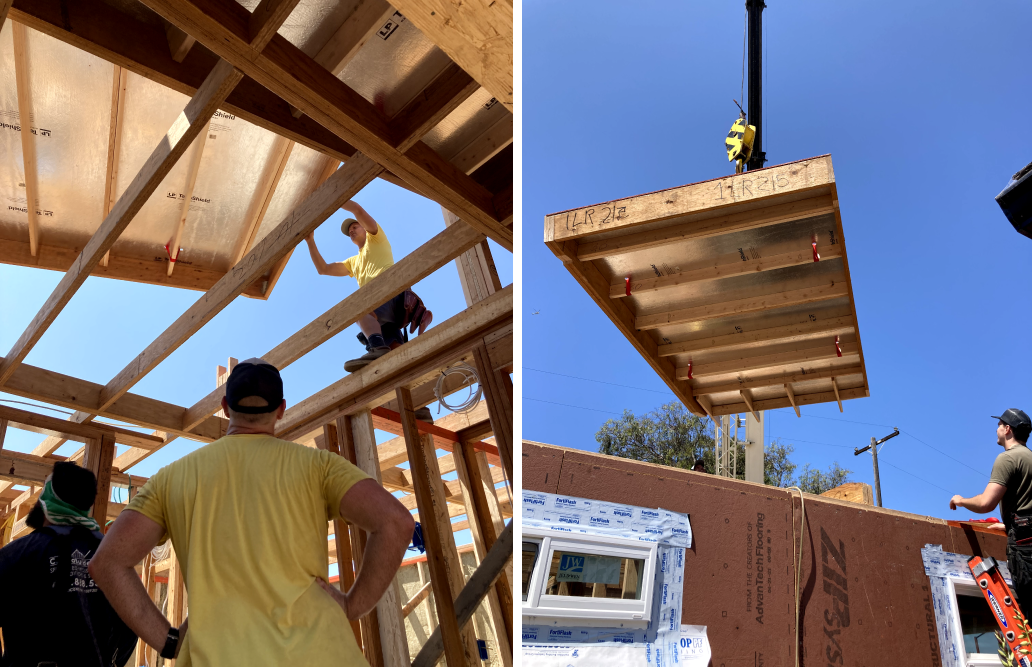
Photo courtesy of Proteus Homes
Because the framework is constructed in a factory with a regular crew of experienced workers, on-site construction moves rather quickly for panelized modular ADUs. Once you sign off on designs, the crew will get started on site prep. In the meantime, your ADU’s panels are being constructed off-site in a factory. Once the pieces arrive at your property, everything is assembled in as little as a day.
From there, finishing the ADU usually takes about three months, depending on the size and design of the unit.
In truth, the timeline for panelized modular ADUs falls in between custom stick builds and traditional prefabs. Although their time frame is not quite as short as traditional prefabs, they do not take nearly as long as custom stick builds (8-10 months).
Custom stick builds require the longest timeline because everything must happen sequentially. In other words, the foundation must be completed before workers can start on the framing. And the framing needs to be done before any finishes can get added.
Traditional prefabs do offer the shortest timeline due to the sheer speed and precision that comes with factory construction. It will still take a few weeks, however, to prep the site and install all the utility connections. From start to finish, it usually takes about a month for a prefab unit to be move-in ready.
It’s important to note that no ADU is immune to supply chain delays or other minor hiccups in the system. But in the end, although going the panelized modular route adds a few months to a traditional prefab timeline, it definitely shaves a few months off a custom stick-built timeline.
For many, this is a big advantage. After all, time is money! And faster construction time means sooner access to all the benefits your ADU has to offer.
Reduced site disruption and waste
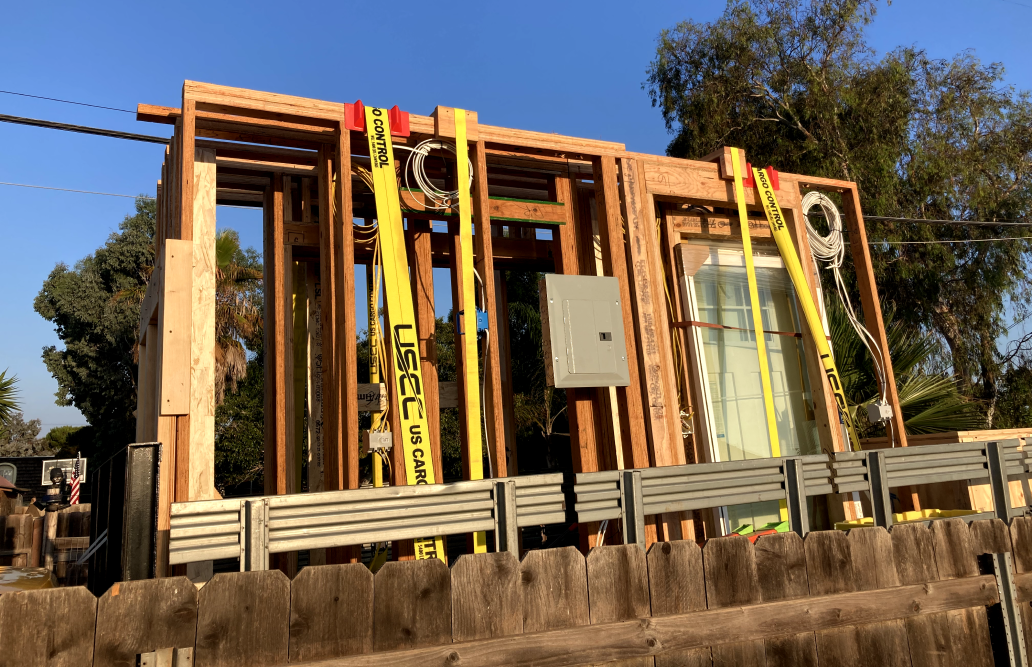
Photo courtesy of Proteus Homes
Besides the time it takes to assemble them on your property, panelized modular ADUs sidestep much of the construction commotion. Reduced noise, stress, on-site construction, disruption to your property…Just imagine! This is the biggest reason homeowners choose prefab options. You can’t put a price on peace of mind!
Compare that to custom stick-built ADUs, where all the construction happens on-site. In that case, anticipate months of noise and the ongoing presence of construction workers. In many ways, your yard becomes a prolonged construction zone. For some homeowners, this is an easy compromise to get the custom ADU of their dreams. But for those who heavily value peace and quiet, this option isn’t as desirable.
Another great reduction with panelized modular ADUs? Waste. With much of the construction taking place in a factory, the lumber is cut by machines that are more precise and less wasteful. This means far less waste ends up in landfills.
Energy efficiency and sustainability
Continuing along the vein of environmentally-friendly practices, panelized modular ADUs offer many ways to promote energy efficiency and sustainability. One such way is by installing structural insulated panels, which significantly cuts down on energy consumption. With the amount of customization choices at your disposal, there are plenty of eco-friendly options to choose from.
Greater precision and quality control
As mentioned earlier, factory machines are more advanced and precise than those used for on-site construction, resulting in greater quality control. Panelized modular ADUs are precision engineered to be air-tight and durable. They’re more than up to the job of withstanding any type of weather Mother Nature throws at them!
How does the cost of panelized modular ADUs compare to other types of ADUs?
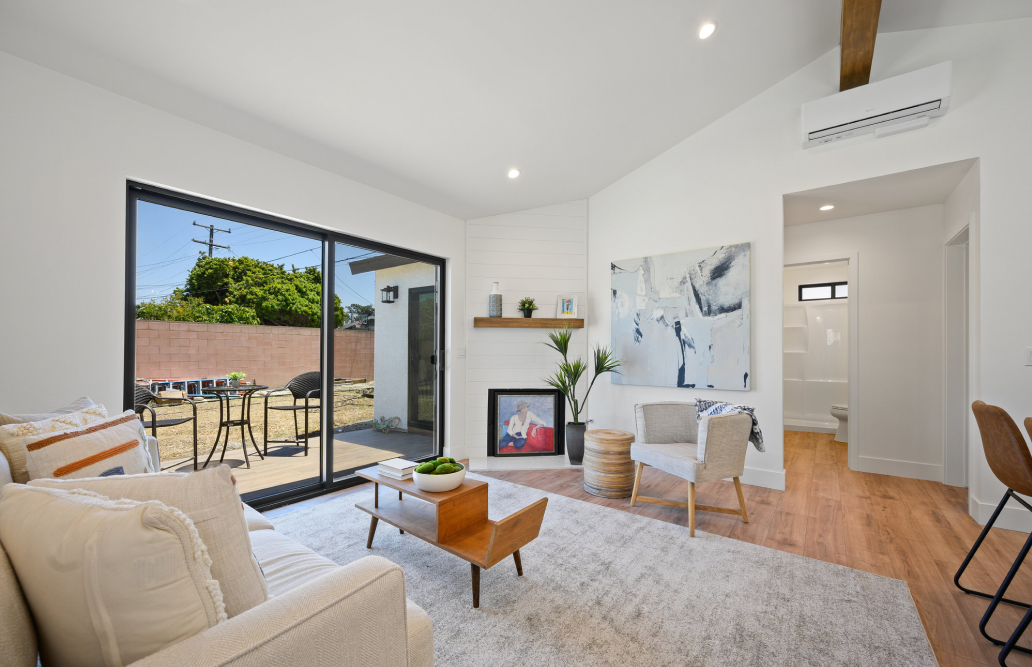
Photo courtesy of Proteus Homes
Ryan Jantz of Proteus Homes, explains it best.
“Panelized modular ADUs are a better value. We definitely have some efficiencies doing the factory builds, but we also use a little bit of higher-end materials, like engineered lumber, so that our walls are perfectly straight. That’s important when you’re trying to crane them in. We spend a little bit more on the materials, but we do save on the efficiency of the build. So, time is definitely the bigger factor than cost savings. That’s where the efficiency really is at.”
In short, panelized modular ADUs cost about the same as traditional construction and traditional prefab, but rest assured that they are built to the highest quality. But the biggest savings you’ll find with this type of build is time.
You can read more about cost comparisons here.
Are panelized modular ADUs durable?
The biggest misconception homeowners have with panelized modular homes is that they lack durability.
Ryan explains:
“People hear ‘panelized’ and they think, ‘Is it going to fall apart or blow over?’ That’s one of the [biggest] objections we face when we’re out selling. But it’s the same 2x4s that you’d have if we were assembling on-site. We just do it in the factory first.”
Rest assured that you are not sacrificing a modicum of quality or durability with a panelized modular ADU. Remember, higher-end materials are used to guarantee the walls are perfectly straight when it comes time to crane them in.
Are panelized modular ADUs completely customizable?
Another common misconception is that panelized modular ADUs will not be able to match the design of the primary home. Again, Ryan offers homeowners the reassurance they need.
“When some people think ‘factory,’ they are thinking ‘mass-produced.’ They think all the same floorplans, walls…that sort of thing. We do try to have some standards as far as window sizes and door sizes that we try to maintain just for simplicity’s sake. But we’re not limited to that. Every home is built to spec per the design of that home. So, we don’t pre-build any wall panels until we have a design from a customer.”
Panelized modular ADUs are extremely flexible builds. Ryan assures homeowners that moving windows, making walls longer, or including any other design elements to duplicate the style of the main home is often totally doable.
How do you choose the right panelized modular ADU company to fit your needs?
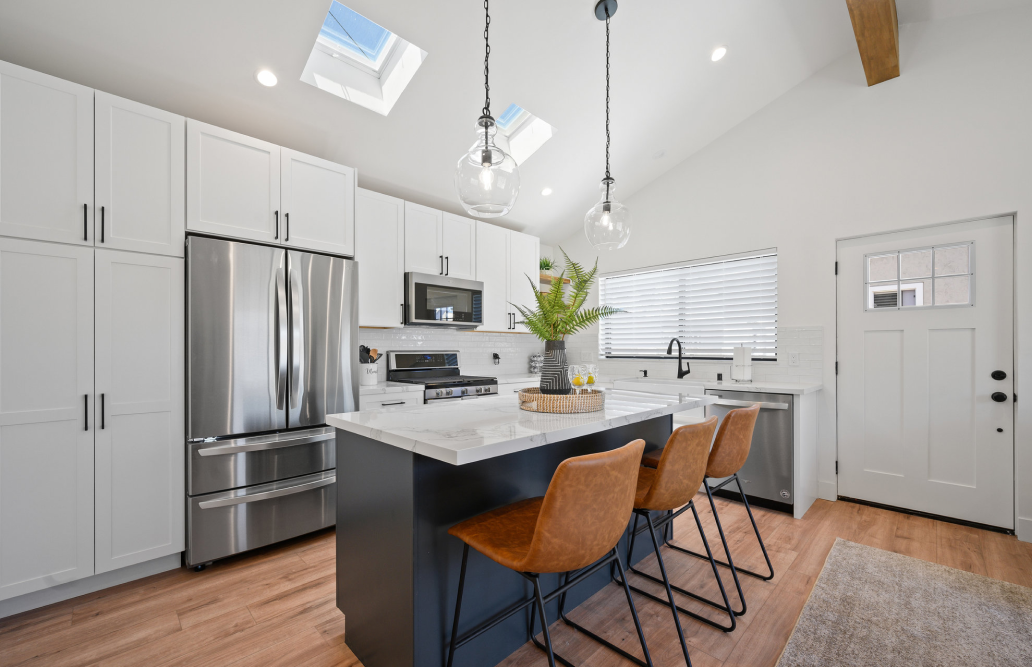
Photo courtesy of Proteus Homes
Deciding what type of ADU you want to build is only the first step of the process. The next is finding the right company to take on your project. Never underestimate the importance of selecting a quality company to handle your ADU construction! Here are some key qualifications to look for.
Communication
We’ve all heard the saying that the key to any successful relationship is good communication, right? Well, it’s really no different when it comes to hiring a company to build your ADU.
A worthy company will maintain open, transparent communication with you. They will firmly understand your budget and ensure that you are involved in the design process so nothing comes as a surprise. While everyone wants desirable features like vaulted ceilings and custom rooflines, it’s not always affordable. The right company will help put things in perspective based on your budget.
Good track record
This may seem obvious, but choosing a company that has a good reputation with panelized modular ADUs is a must! The last thing you want is to put your project in the hands of a company that doesn’t have a good track record for turning out this type of ADU.
Make sure you do your research, and choose a company that has a proven work history of being more than capable to execute a project like this.
Variety in options
It is helpful to have flexibility when it comes to designing your ADU. For example, a company with a variety of floorplans, finishes, exterior designs, and more to choose from will certainly come in handy when the time comes to turn your ADU vision into a reality.
Contact Maxable to get matched to a panelized modular company
At Maxable, we understand the importance of quality, experience, and reliability. To guarantee that you don’t go wrong with a panelized modular company, we’re a great resource to take advantage of!
With our vetted network of designers and builders, we’ll make sure that you get paired with nothing less than the best. Contact us today to find the right company for you!
What is the process of building a panelized modular ADU?

Photo courtesy of Proteus Homes
Panelized modular ADUs have expedited timelines, making them a highly desirable option for many homeowners. But it’s still important to know what to expect throughout the entire process. To give you a better idea, let’s break down the different stages.
Design and planning
First things first, you need to come up with a design plan. This is where you map out your vision for the ADU. While there are some basic floor plans to choose from, you could also go the semi-customization route that we mentioned earlier. Homeowners usually find this approach easier, more efficient, and cost-effective.
And if you want to go all out with customization, have at it! Some companies will even let you bring in design plans from your own architect. Just remember that this option will extend the overall timeline and budget.
Manufacturing and transportation
Now that the design plans are in place, it’s time for your panelized prefab company to get building. All the pieces that will eventually make up your ADU will be constructed in their factory using advanced precision tools.
Once all the panels are built, they will be loaded onto a flatbed truck and delivered to your property. And no need to stress about transportation! Panelized modular ADUs are extremely durable, often more so than even custom stick builds so that they can withstand the 50-60 miles per hour down a highway to your property.
Site-prep
Site prep usually takes place while the panels are being constructed in the factory, so your timeline is already on the fast track.
This part of the process often takes a few weeks. No matter what kind of ADU you’re building, the site will need to be prepared. This may include demolishing an existing structure (e.g., a garage) or removing trees to clear space for the ADU.
All prefabs will also require a poured cement foundation. If you’re doing a garage conversion custom ADU, you’re in luck! You might be able to use the existing foundation and save some money.
On-site assembly and installation
Next is the on-site assembly of your ADU. This stage can often be done in a single day. Incredible!
The panels will be set into place on the new foundation, either with a crane or manually.
Insulation, drywall, and utilities
Now that everything is assembled, the rest is similar to traditional construction. The construction crew will install the insulation, drywall, windows, etc. During this time, utilities are connected as well.
Finishing touches
All that’s left is to install things like cabinets, showers, toilets, flooring, and more.
After that, it’s time to say hello to your brand-new ADU!
Is a panelized modular ADU right for you?
Seeking professional guidance and support
Talking to experts in the field who can offer you professional guidance and support is a smart move. They will have inside knowledge to share with you and may point out factors you hadn’t considered before. Let them talk you through what adding a panelized modular ADU would mean for you.
Contact Maxable
Speaking of professional guidance and support, are you in need of some advice? No problem. We look forward to talking through panelized modular ADUs with interested homeowners. Together, we’ll help you weigh your options and discuss what makes sense for you.
Plan, hire, and manage your ADU project with Maxable!
Ready to get started? Let the process begin with Maxable.
Tell us about your ADU plans! Based on your location, budget, needs, and dreams, we’ll match you to a complete team of ADU professionals that will launch your project off the ground (that includes panelized modular companies too ;)
Maxable has already matched hundreds of homeowners to their ADU dream teams. Become our next ADU success story today.